i should like to go and see some of these fabrics in production
Mr. Kanai says the mud-dyeing process alone takes more than a month, as the silk is first colored a burgundy hue with natural dye made from the pulp of a local plum tree. Getting the right shade of red requires repeating the cycle of staining and drying the silk 30 times, he said. Only then is the silk ready to be immersed in the black mud, whose iron reacts with tannins in the tree dye to create the coveted dark brown color.That is not the most elaborate step. Even before the silk arrives at Mr. Kanai�s workshop, it is first woven into a temporary fabric as part of a unique method that the islanders have devised for creating minutely detailed patterns. After this temporary fabric has been mud-dyed, it is unraveled back into its original silk threads. Each colored thread now has thousands of tiny white stripes where it overlapped with another thread, blocking the mud from touching it at that point
As the threads are rewoven into new fabric by nimble-fingered island women, they slowly reveal perfectly formed patterns, ranging from starkly minimalist shapes to elaborate scenes of bamboo groves and flying storks.
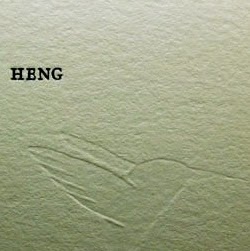